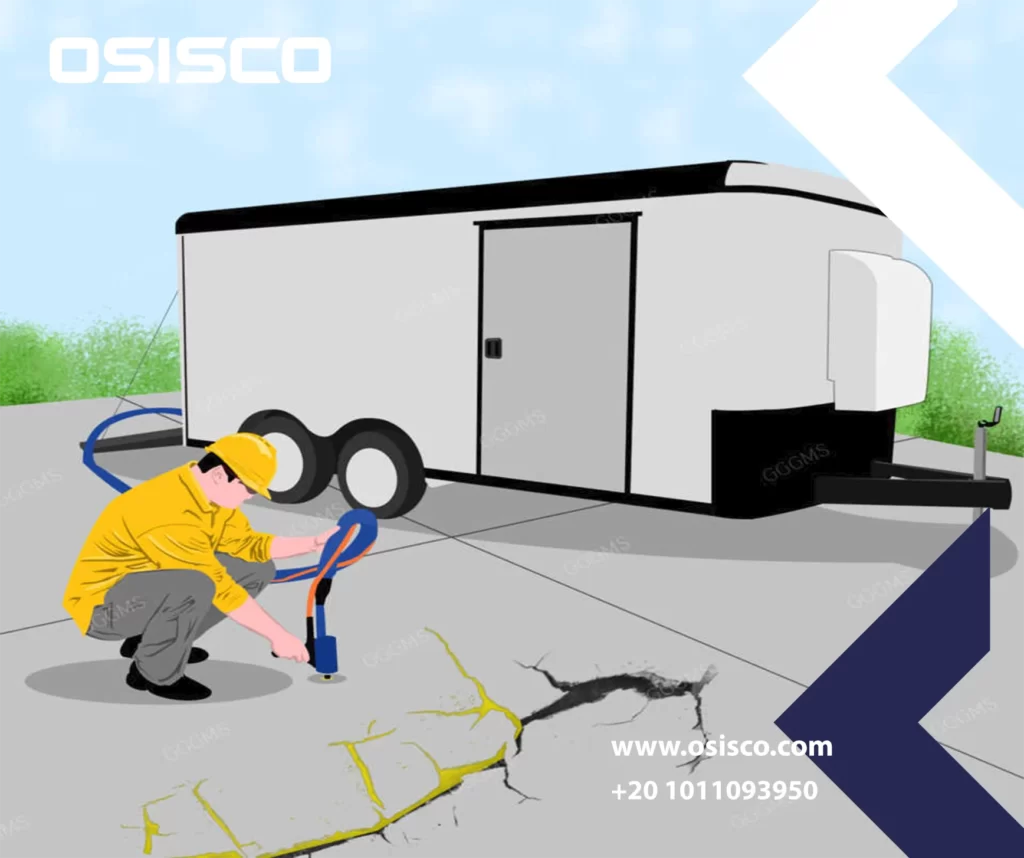
Injection hoses are used as a planned joint insert for sealing construction joints, butt joints, or block joints in structural engineering, civil engineering, and tunnel construction.
Hose systems show their advantages not only in heavily reinforced components or in complicated geometries.
In addition to conventional joint sealing systems, they can also serve as an additional “insurance policy” for leaks in the joint that occur years later, which can otherwise only be sealed with much greater effort.
In simple terms, in an injection hose system, a hose perforated with special slots is applied to the area of the subsequent joint using clamps before the concrete is poured, the ends of the hose are closed and stored so that they are still accessible after pouring.
Injection of grouting hoses with acrylate gel
The systematically installed injection hoses into the construction joints get grouted after the atrophy of the concrete is finished.
The first set of concrete is presumed. During the shrinkage process of the concrete, a joint is built up around the hose, which secures successful grouting of the same. These problems appear while compacting the fresh concrete, resulting in gaps and cavities that can be combed out.
Acrylate gel is characterized by a high elongation at break, high mechanical stability, and rubber-elastic behavior. Therefore, it is used for veil, surface, or crack injections and compression of injection hoses.
Injection of grouting hoses with polyurethane resin
Represents an effective method of improvement of mechanical and sealing properties of soil and rock environment and constructions, hardens and connects the disintegrated parts of the rock mass or grains of loose material.
Polyurethane grouting technologies spread significantly from mining applications to civil engineering and geotechnics. .
The principle of grouting technologies is the injection of liquid grouting material into the rock environment or construction under pressure.
During the grouting process, fissures and pores are filled with the grouting material, which subsequently.
Grouting – structure
Structures of any kind need to be supported by the soil and bedrock beneath them. While this concept may seem obvious, the subsurface conditions are not.
Ground improvement is often needed to increase the bearing capacity or provide settlement control for new construction or remedy an existing issue.
Helical Drilling provides many ground improvement solutions, two of which are the grouting techniques compaction grouting, and jet grouting.
Purpose of grouting hoses
The purpose of grouting can be either to strengthen a formation or to reduce water flow through it. It is also used to correct faults in concrete and masonry structures.
grouting techniques
- Compaction Grouting.
- Slurry Grouting.
- Permeation Grouting.
- Chemical Grouting.
- Jet grouting.
We can use the previous techniques to improve the soil and to repair the different element structures in general such as tunnels, Bridges, Dams, Residential buildings, including foundations and swimming pools, and Underground structures.