The concrete Cracking injection brings back the crack together and helps restore the strength of a structure. The repair strength of these injections happens to be stronger than that of concrete.
The solution also prevents movement of the concrete that takes place during natural expansion and provides the concrete with the potential to create more structural stability and strength, next we will know more about it with OSISCO.
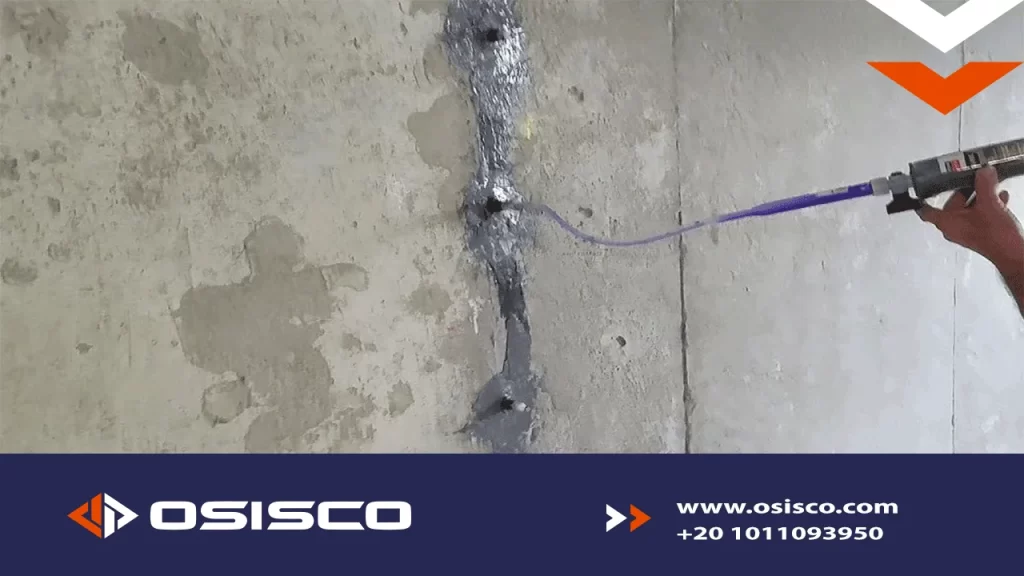
These cracks may initially be too small to be detected and to have any negative consequences at first, while at other times, never grow to be a problem at all.
Cracking injection Types
Other cracks become visible very early and cause problems, such as water leakage, almost immediately. Even the early undetected cracks can, in time, become larger and cause problems, whether structural or more commonly a source of water leakage.
This can be determined as follows:
- Especially in colder climates, moisture can permeate these tiny breaks in the concrete substrate and enlarge them to full-fledged leaking cracks by moisture expansion/contraction resulting from freeze/thaw cycle of the moisture.
- In addition, as the ground around the foundation stabilizes, any movement can cause the rigid concrete substrate to separate these tiny breaks in the concrete, enlarging then to a water- leaking size.
- A more serious problem to solve is when the area around the foundation remains unsettled, resulting in ongoing stress on the concrete structure. If this stress exceeds the strength of the concrete, cracks will form even where initial cracks did not exist (even after repair of these initial cracks).
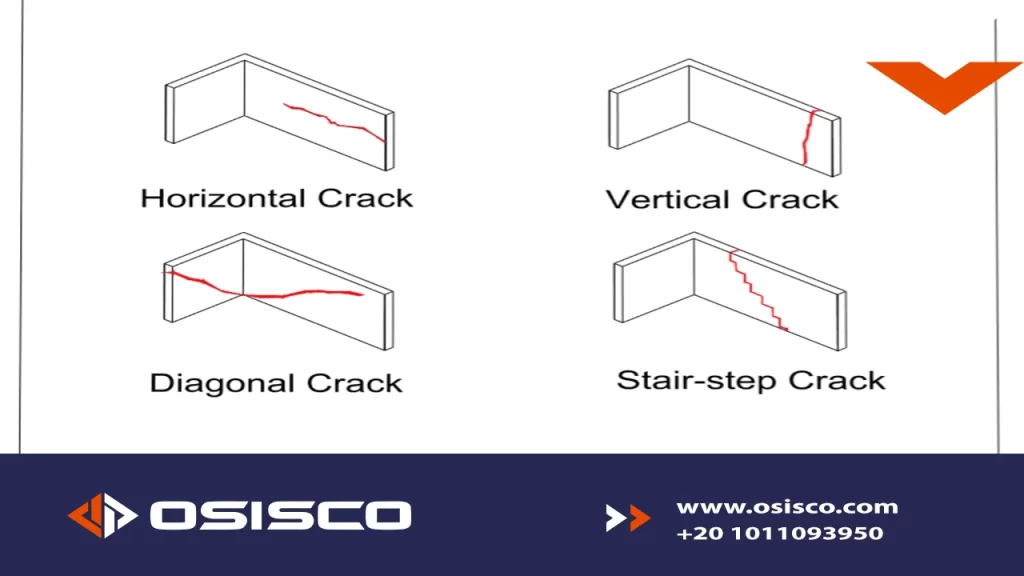
Polyurethane elastomeric foams, when concrete structural integrity is not a problem and the problem is only water leakage.
Polyurethane foams harden very rapidly (unlike most epoxies) and are less likely to flow out the back of
some cracks as epoxies may.
Furthermore, polyurethane foams expand in the crack area and may reach areas that an epoxy may not, if not
properly injected.
You can also know more about crack injection system.
Polyurethane, being elastomeric, may also handle concrete movement more effectively than the more rigid epoxies (although this is a debated point).
The secret to effective Cracking injection, whether epoxies or polyurethanes, is patient, low-pressure introduction of the liquid into the cracks, low pressure (20-40 PSI) allows the applicator to properly monitor the Cracking injection process.
At this pressure range, the applicator can be confident that the crack has been saturated with the liquid polymer until the liquid begins to collect at an adjacent surface port.
If done at higher pressure, the liquid polymer may only be filling the larger
sections of the crack, leaving smaller crack sections available for future
deterioration.
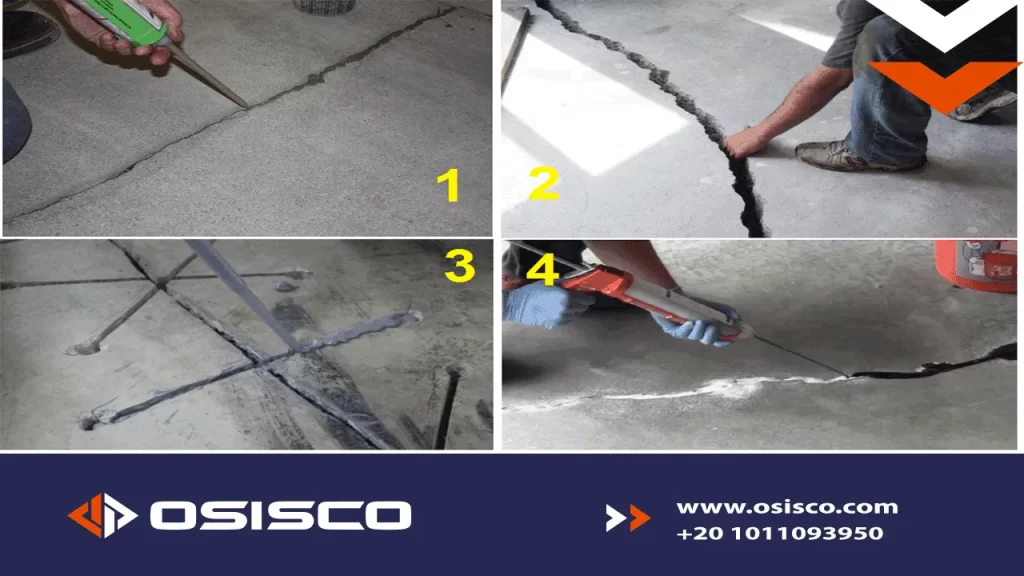
Our company is characterized by the completion of similar works perfectly with the presence of highly experienced engineers with trained labor, equipment, and materials. We are also distinguished by the speedy completion of our commissioned work.
The development of dual cartridge dispensing, utilizing either disposable or re-usable dual cartridges or containers, has significantly simplified the equipment and power requirements.
It is now possible to utilize manual dispensing tools similar to caulk guns to inject both epoxies and polyurethane systems.
It is important to note that it is best to choose such equipment which utilizes a spring to control the injection pressure.
Other manual tools, without the spring as a control, can easily cause injecting at a pressure much higher than desired. This may result in the incomplete injection of a crack, the most common reason for crack repair failure.
Air-powered equipment is also available to do Cracking injection via dual cartridge dispensing. It is important that this equipment have means of controlling injection pressure to 20-40 PSI.
Air powered equipment makes it feasible to use larger containers, which may reduce the overall cost of the liquid polymer system.
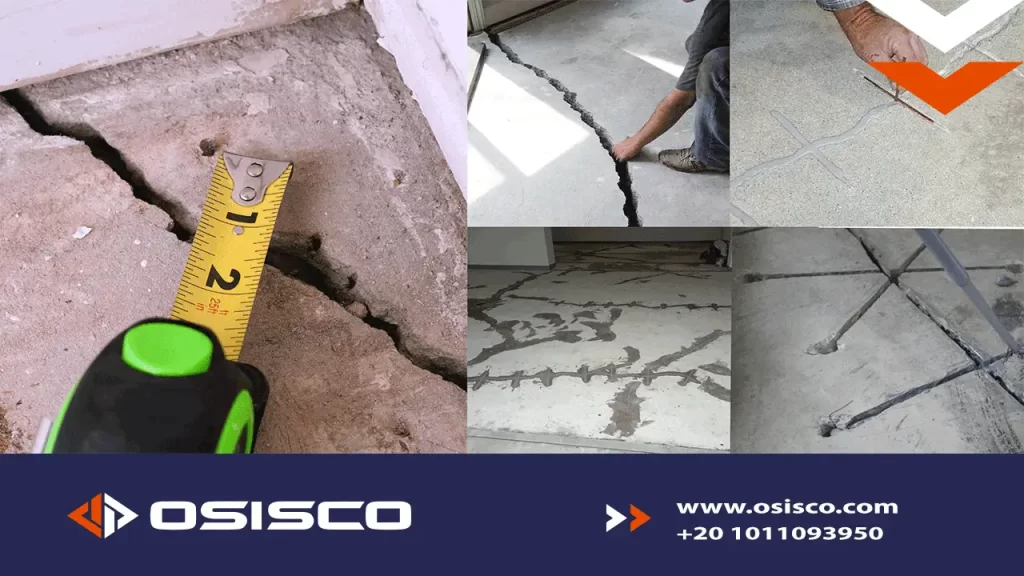
Low pressure injection
Low-pressure Cracking injection systems are becoming increasingly popular as the method of choice to repair leaky cracks in poured foundation walls. The days of digging, chipping, and drilling are long gone as these easy-to-use injection systems allow for the repair and waterproofing of most foundation cracks from the inside using simple hand tools.
Today, both epoxy and polyurethane resin are available in cartridge-style systems that can be used with standard caulking guns or dual-cartridge dispensing tools.
Both systems will effectively fill the crack while keeping water out. Does the choice now become which system to use? Often a contractor will develop a preference for one injection system over another, just like some prefer wood to fiberglass hammer handles. Many times, the best tool for the job is the one that works best for you.
Epoxy Injection is traditionally used to weld cracked concrete back together to restore the structural integrity of the concrete wall. Epoxies are available in very low viscosities that make them ideal for injecting hairline cracks.
Epoxy’s high-strength bonding ability makes them a clear choice for repairs such as concrete that cracked during backfilling. Polyurethanes are available in one or two-part liquid resins that chemically react with available moisture and foam up and create a flexible seal inside the crack.
They can even seal off the outside of the crack which can be preferable in porous or loose soil conditions. Polyurethane foam is ideal for filling wider cracks and cracks that may exhibit signs of settling or movement from changing seasons and soil pressures. Polyurethane also works great for filling in voids or sealing leaks around pipe penetrations.
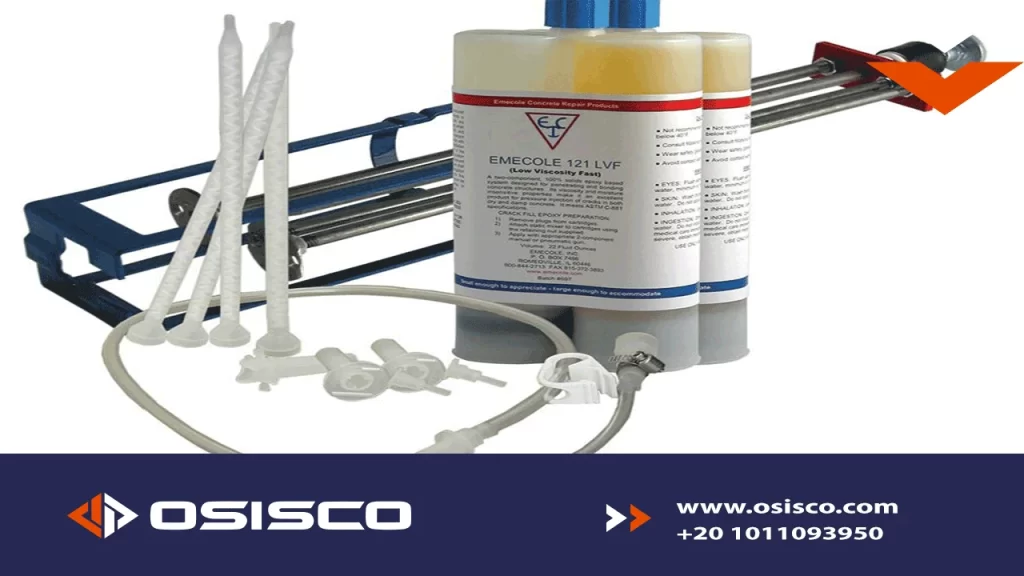
Installation of Low pressure injection
Both systems can be installed in less than one hour and can be used conveniently from the inside of the basement. This eliminates the need for digging up the outside foundation, which can be disruptive, time-consuming, and costly.
Both resin systems are available in single 10-ounce caulking style cartridges or dual side-by-side cartridges and injected with low-pressure hand dispensing tools.
Both systems are equally suited for typical foundation cracks, but epoxy injection is best installed in dry cracks while polyurethane resin systems are moisture reactive and may actually require the crack to be pre-wet with a small amount of water in order to activate the full expansion of the resin.
High-pressure injection
High-pressure injection involves inserting a liquid into a very narrow crack, The required equipment was specially designed by a highly qualified technician to infiltrate any type of crack with a 100% efficiency rate. The technician’s work involves regulating the flow, as well as the pressure of the liquid in the concrete crack for a lasting final result.
In the residential sector, the resistance of concrete on a wall or foundation floor is approximately 20-25 MPA or 2900-3625 psi. In the event that the pressure is unable to reach a minimum of 2500 psi or exceed 3500 psi, you would get poor quality work and assured inefficiency.
It is important to remember that too much flow and too much pressure will create micro-cracks in the concrete and around the injection port, where the liquid will escape instead of infiltrating the crack.
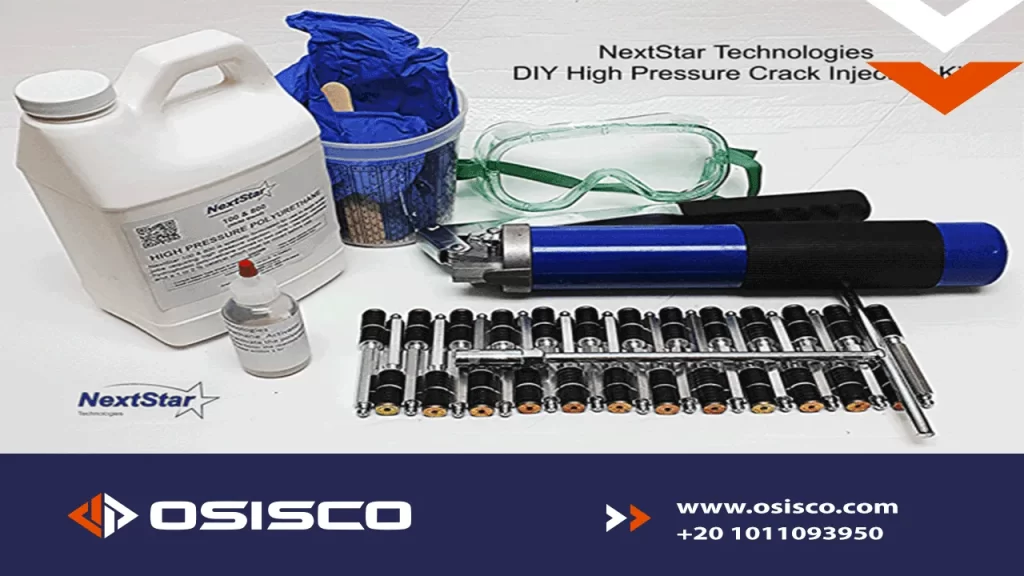