Soil nailing is generally classified as a method of soil improvement in cutting, during which a quasi-homogeneous body is created. The method consists of the installation of nails into soil body. The nails are generally steel bars or pipes that are inserted into the drill hole and grouted or driven into the soil using different technologies.
Soil reinforcement and soil nailing, are very similar, but significant differences can be seen in their deformation, mainly due to different technologies of construction, when the reinforced soil is constructed from the bottom up and while soil nails the other way around, Soil nailed wall, constructed from top to bottom, has the biggest deformation both horizontal and vertical at the top of the wall.
whereas geosynthetic reinforced soil has the biggest deformations at the bottom part due to the highest load from the upper layers.
Soil nailing consists of the passive reinforcement of existing ground by installing closely spaced steel bars which may be subsequently encased in grout. As construction proceeds from the top to bottom, shotcrete is also applied on the excavation face to provide continuity.
The origin of soil nailing can be traced to a support system for underground excavations in rock referred to as the New Austrian Tunneling Method. This tunneling method consists of the installation of passive steel reinforcement in the rock followed by the application of reinforced shotcrete.
Soil Nail Application
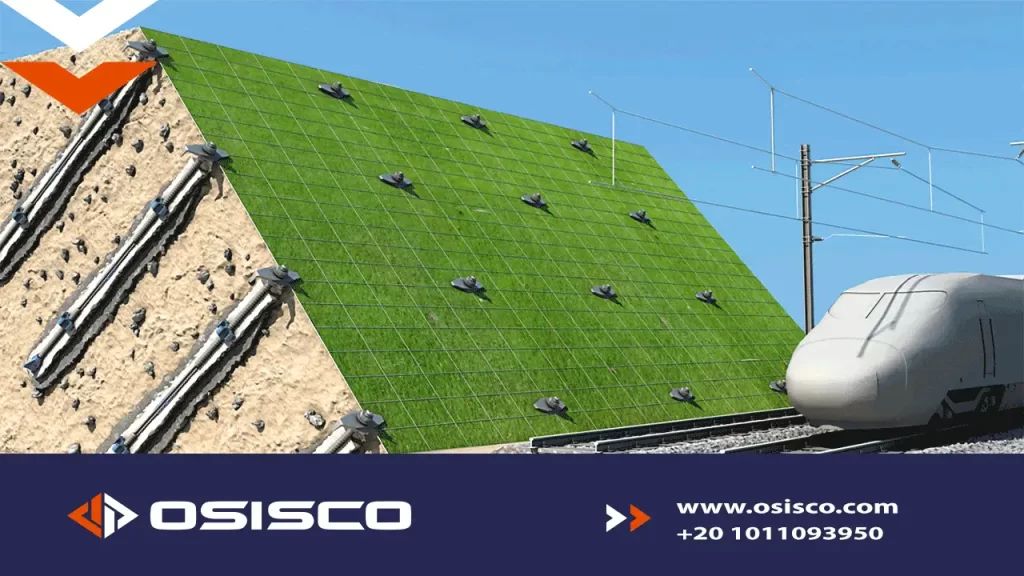
Slope stabilization by nailing at a railway abutment in Säo Paulo, Brazil:
Advantages of soil nailing
- Economy: The cost of soil nailing is maybe 50% of a tieback wall.
- Rate of construction: Fast rates of building.
- Facing inclination: Easily accommodates an inclined facing, benefiting overall stability.
- Deformation behavior: 0.1 to 0.3 % of the wall height for well-designed walls.
- Design flexibility
- Design reliability in saprolite soils: saprolite soils frequently present relict weak surfaces which can be undetected during site investigation.
you can know more about Foam soil stabilization
Disadvantages of soil nailing
- Soil nail walls may not be appropriate for applications where very strict deformation control is required for structures and utilities located behind the proposed wall, as the system requires some soil deformation to mobilize resistance. Deflections can be reduced by post-tensioning but at an increased cost.
- Existing utilities may place restrictions on the location, inclination, and length of soil nails.
- Soil nail walls are not well-suited where large amounts of groundwater seep into the excavation because of the requirement to maintain a temporary unsupported excavation face.
- Permanent soil nail walls require permanent, underground easements.
- Construction of soil nail walls requires specialized and experienced contractors.
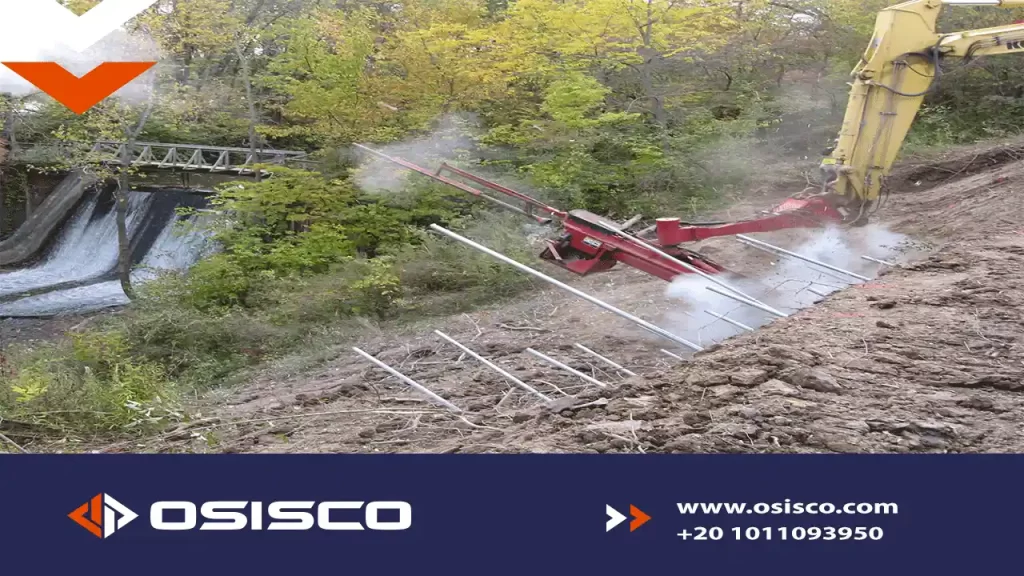
Soil nailing is typically used to stabilize slopes or excavations, where the top/down structure is more advantageous in comparison with other retaining wall systems. In certain circumstances, soil nailing is an applicable alternative in comparison with ground anchor walls used in commonly preferred top/down fixing system in terms of technical feasibility, construction costs, and construction period.
Installation Methods for soil nailing
1- Drill and grout:
A soil-nail reinforcement is inserted into a pre-drilled hole, which is then cement-grouted under gravity or low pressure.
Construction Sequence:
- Drilling Holes for Soil Nails.
- Grouted soil nails.
- Preparation of Wall Face.
- Shotcrete Application.
2- Self – drilling:
The soil-nail reinforcement is directly drilled into the ground using a sacrificial drill bit. The reinforcement, which is hollow, serves as both the drill rod and the grout pipe.
Hollow-core soil nail installation and grout paths.
Schematic of a cross-section of hollow-core soil nail and the grout body
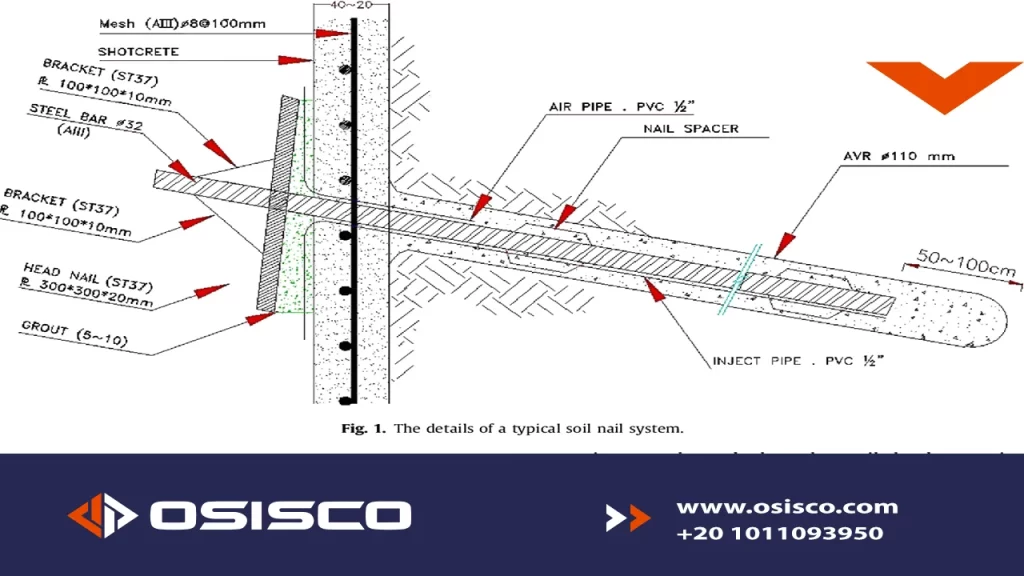
3- Driven:
Soil-nail reinforcement is directly driven into the ground by the ballistic method using a compressed air launcher, by the percussive method using hammering equipment, or by the vibratory method using a vibrator.
Launched nails are bars “launched” into the soil at high speeds approaching 200 miles per hour using a firing mechanism involving compressed air.
Bars can be perforated galvanized steel tubes, perforated fiberglass, or bare steel tubes. Bars are typically 1.5 in. in diameter and can be 2 in. in diameter. They can be up to 20 ft in length.
Main Components for soil nailing system
- Nail head details for vertical or near vertical walls.
- Nail head details for inclined slopes.
- Typical PVC centralizers are attached to a solid bar.
- Typical steel centralizers.
- Threaded solid tendon with steel plate, and nut.
- Solid tendons with gray and purple epoxy coating (left) and partially encapsulated by corrugated sheathing (right).
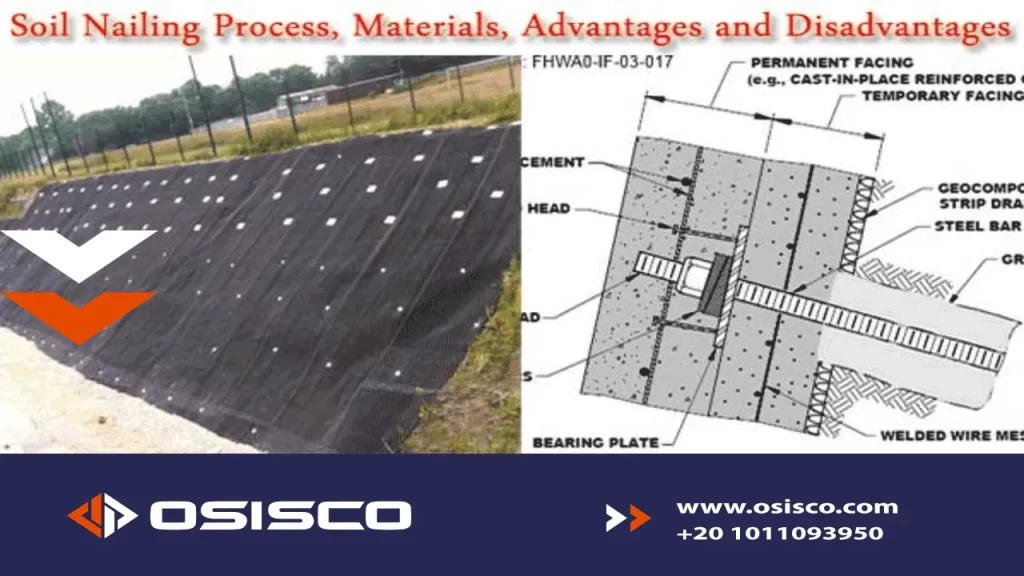
Facing connection
Soil Nail Vertical and Horizontal Spacing:
- Nail Square Pattern.
- Nail Staggered Pattern.
Initial Facing
- Initial shotcrete application.
- Shotcrete reinforcement including panels or sheets and waler bars.
Final Facing
In principle, the soil nailed wall behaves as monolith and basically it acts as a gravity wall. Therefore, its design has two phases.
1- External stability:
Stability of this monolithic block, checking the bearing capacity, overturning, sliding and overall stability along slip surface outside of soil nailed block.
2- Internal stability:
For tensile failure of nails and its pull-out from soil in theory we have to check also the case of shear failure between nail and grout and between grout and soil.
Modes of failure for soil nailing
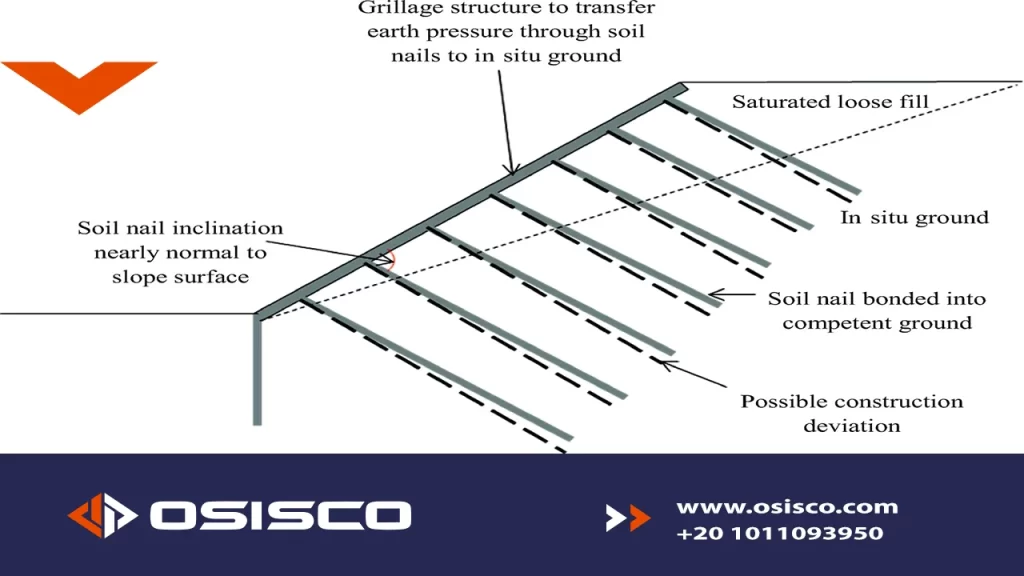
- External Failure Modes.
- Internal Failure Modes.
- Facing Failure Modes.
- Internal Stability.
- External Stability.
Soil Nailing Testing
Hydraulic Jack Used for Soil Nail Load Testing:
It should also be noted that the long-term performance of shotcrete facings has not been fully demonstrated, particularly in areas subjected to freeze-thaw cycles. In these circumstances it is recommended that the design prevents frost from penetrating the soil by provision of an appropriate protective structure Special attention must be paid in both the design and the construction stage to the issue of corrosion and durability of the structural elements.
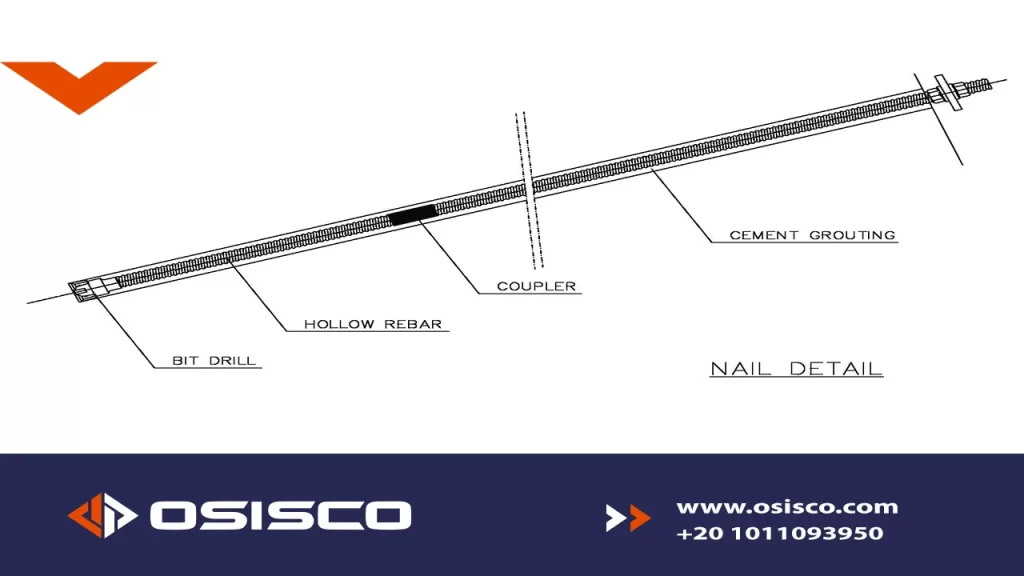